Chemical Upcycling of Waste Polyethylene Terephthalate via Cosolvent-Assisted Alkaline Hydrolysis
DOI:
https://doi.org/10.29356/jmcs.v69i3.2206Keywords:
PET, chemical upcycling, alkaline hydrolysis, TPA, energy economy coefficientAbstract
Abstract. Alkaline hydrolysis is a chemical recycling process for depolymerizing waste polyethylene terephthalate (PET) into monomers. These monomers can be used as a starting material to produce PET with the same quality as the original polymer. But conventional alkaline hydrolysis is carried out at a high temperature for a long reaction time which increases the capital and operating cost of the overall process. Therefore, developing an efficient method for PET depolymerization under mild reaction conditions is necessary to make upcycling an economically attractive process. In this work, the alkaline hydrolysis of waste PET was carried out with n-propanol as a co-solvent under mild conditions (70 °C). Sodium hydroxide (NaOH) was used as a catalyst. The effects of process parameters such as reaction time (15-60 min), co-solvent volume ratio (20 %, 40 %, and 60 %), and NaOH concentration (5 % and 15 % wt/vol) were examined on PET conversion and monomer (terephthalic acid (TPA)) yield. At optimal conditions (60:40 vol% n-propanol: H2O, 15 wt% NaOH, 70 °C, 45 minutes), %PET conversion and %TPA yield obtained was 91.4 % and 71.3 %, respectively. Differential scanning calorimetry (DSC), powder X-ray diffraction (p-XRD), thermogravimetric analysis (TGA), nuclear magnetic resonance spectroscopy (NMR) and Fourier-transform infrared spectroscopy (FTIR) were used to assess the purity of the produced TPA. PET depolymerization kinetics was studied with the help of solid-state kinetic models. The best-fit kinetic models were a first-order reaction, geometrical contraction, and one-dimensional diffusion models. The energy economy coefficient, energy metrics, was used to compare the performance of n-propanol as a co-solvent with other co-solvents reported in the literature. It was found that n-propanol as a co-solvent is as efficient as ethanol at high NaOH concentration (15 wt/vol%).
Resumen. La hidrólisis alcalina es un proceso de reciclaje químico utilizado para despolimerizar residuos de polietilentereftalato (PET) en monómeros. Estos monómeros pueden emplearse como materia prima para producir PET con la misma calidad que el polímero original. Sin embargo, la hidrólisis alcalina convencional se lleva a cabo a alta temperatura y durante un tiempo prolongado de reacción, lo que incrementa los costos de inversión y operación del proceso. Por ello, es necesario desarrollar un método eficiente para la despolimerización del PET bajo condiciones suaves de reacción, a fin de que el reciclaje ascendente sea un proceso económicamente atractivo. En este trabajo, la hidrólisis alcalina de residuos de PET se realizó utilizando n-propanol como cosolvente bajo condiciones suaves (70 °C). Se utilizó hidróxido de sodio (NaOH) como catalizador. Se estudiaron los efectos de parámetros del proceso como el tiempo de reacción (15-60 minutos), la proporción de volumen del cosolvente (20 %, 40 % y 60 %) y la concentración de NaOH (5 % y 15 % peso/volumen) sobre la conversión del PET y el rendimiento de monómero (ácido tereftálico, TPA). En las condiciones óptimas (60:40 % vol n-propanol:agua, 15 % peso/vol NaOH, 70 °C, 45 minutos), se obtuvo un 91.4 % de conversión de PET y un 71.3 % de rendimiento de TPA. Se utilizaron calorimetría diferencial de barrido (DSC), difracción de rayos X en polvo (p-XRD), análisis termogravimétrico (TGA), espectroscopía de resonancia magnética nuclear (RMN) y espectroscopía infrarroja por transformada de Fourier (FTIR) para evaluar la pureza del TPA producido. La cinética de despolimerización del PET se estudió con la ayuda de modelos cinéticos en estado sólido. Los modelos cinéticos que mejor se ajustaron fueron el de reacción de primer orden, contracción geométrica y difusión unidimensional. El coeficiente de economía energética, o métricas energéticas, se utilizó para comparar el desempeño del n-propanol como cosolvente con otros cosolventes reportados en la literatura. Se encontró que el n-propanol como cosolvente es tan eficiente como el etanol a una alta concentración de NaOH (15 % peso/vol).
Downloads
References
Global Plastics Outlook, OECD, 2022. DOI: https://doi.org/10.1787/de747aef-en.
de Dios Caputto, M.D.; Navarro, R.; Valentín, J. López; Marcos-Fernandez, A. J. Clean. Prod. 2024, 454, 142253. DOI: https://doi.org/10.1016/j.jclepro.2024.142253.
Geyer, R.; Jambeck, J.R.; Law, K.L. Sci. Adv. 2017, 3, e1700782. DOI: https://doi.org/10.1126/sciadv.1700782.
Joseph, T. M.; Azat, S.; Ahmadi, Z.; Jazani, O. M.; Esmaeili, A.; Kianfar, E.; Haponiuk, J.; Thomas, S. Case Stud. Chem. Environ. Eng. 2024, 9, 100673. DOI: https://doi.org/10.1016/j.cscee.2024.100673.
Jambeck, J.R.; Geyer, R.; Wilcox, C.; Siegler, T.R.; Perryman, M.; Andrady, A.; Narayan, R.; Law, K.L. Science. 2015, 347, 768–771. DOI: https://doi.org/10.1126/science.1260352.
Shojaei, B.; Abtahi, M.; Najafi, M. Polym. Adv. Technol. 2020, 31, 2912–2938. DOI: https://doi.org/10.1002/pat.5023.
Rahimi, A.; García, J.M. Nat. Rev. Chem. 2017, 1, 0046. DOI: https://doi.org/10.1038/s41570-017-0046.
Sinha, V.; Patel, M.R.; Patel, J.V. J. Polym. Environ. 2010, 18, 8–25. DOI: https://doi.org/10.1007/s10924-008-0106-7.
Thiounn, T.; Smith, R.C. J. Polym. Sci. 2020, 58, 1347–1364. DOI: https://doi.org/10.1002/pol.20190261.
Raheem, A.B.; Noor, Z.Z.; Hassan, A.; Abd Hamid, M.K.; Samsudin, S.A.; Sabeen, A.H. J. Clean. Prod. 2019, 225, 1052–1064. DOI: https://doi.org/10.1016/j.jclepro.2019.04.019.
Barnard, E.; Rubio Arias, J.J.; Thielemans, W. Green Chem. 2021, 23, 3765–3789. DOI: https://doi.org/10.1039/D1GC00887K.
Chen, H.; Wan, K.; Zhang, Y.; Wang, Y. ChemSusChem. 2021, 14, 4123–4136. DOI: https://doi.org/10.1002/cssc.202100652.
Zhao, Y.B.; Lv, X.D.; Ni, H.G. Chemosphere. 2018, 209, 707–720. DOI: https://doi.org/10.1016/j.chemosphere.2018.06.095.
Vollmer, I.; Jenks, M.J.F.; Roelands, M.C.P.; White, R.J.; Harmelen, T.; Wild, P.; Laan, G.P.; Meirer, F.; Keurentjes, J.T.F.; Weckhuysen, B.M. Angew. Chem. Int. Ed. 2020, 59, 15402–15423. DOI: https://doi.org/10.1002/anie.201915651.
Jehanno, C.; Alty, J.W.; Roosen, M.; De Meester, S.; Dove, A.P.; Chen, E.Y.X.; Leibfarth, F.A.; Sardon, H. Nature. 2022, 603, 803–814. DOI: https://doi.org/10.1038/s41586-021-04350-0.
Olazabal, I.; Luna Barrios, E.J.; De Meester, S.; Jehanno, C.; Sardon, H. ACS Appl. Polym. Mater. 2024, 6, 4226–4232. DOI: https://doi.org/10.1021/acsapm.4c00326.
Hu, L.C.; Oku, A.; Yamada, E.; Tomari, K. Polym. J. 1997, 29, 708–712. DOI: https://doi.org/10.1295/polymj.29.708.
Kosmidis, V.A.; Achilias, D.S.; Karayannidis, G.P. Macromol. Mater. Eng. 2001, 286, 640–647. DOI: https://doi.org/10.1002/1439-2054(20011001)286:10<640::AID-MAME640>3.0.CO;2-1.
Karayannidis, G.P.; Chatziavgoustis, A.P.; Achilias, D.S. Adv. Polym. Technol. 2002, 21, 250–259. DOI: https://doi.org/10.1002/adv.10029.
Mishra, S.; Zope, V.; Goje, A. Polym. Int. 2002, 51, 1310–1315. DOI: https://doi.org/10.1002/pi.873.
Mishra, S.; Goje, A.S. Polym. React. Eng. 2003, 11, 963–987. DOI: https://doi.org/10.1081/PRE-120026382.
Khalaf, H.I.; Hasan, O.A. Chem. Eng. J. 2012, 192, 45–48. DOI: https://doi.org/10.1016/j.cej.2012.03.081.
Ügdüler, S.; Van Geem, K.M.; Denolf, R.; Roosen, M.; Mys, N.; Ragaert, K.; De Meester, S. Green Chem. 2020, 22, 5376–5394. DOI: https://doi.org/10.1039/D0GC00894J.
Panda, D.; Patra, S.; Awasthi, M.K.; Singh, S.K. J. Chem. Educ. 2020, 97, 1101–1108. DOI: https://doi.org/10.1021/acs.jchemed.9b00337.
Cosimbescu, L.; Merkel, D.R.; Darsell, J.; Petrossian, G. Ind. Eng. Chem. Res. 2021, 60, 12792–12797. DOI: https://doi.org/10.1021/acs.iecr.1c02604.
Parab, Y.S.; Shukla, S.R. J. Macromol. Sci. Part A. 2013, 50, 1149–1156. DOI: https://doi.org/10.1080/10601325.2013.830004.
Ravichandran, S.A.; Rajan, V.P.; Aravind, P.V.; Seenivasan, A.; Prakash, D.G.; Ramakrishnan, K. Macromol. Symp. 2016, 361, 30–33. DOI: https://doi.org/10.1002/masy.201400269.
Khawam, A.; Flanagan, D.R. J. Phys. Chem. B. 2006, 110, 17315–17328. DOI: https://doi.org/10.1021/jp062746a.
Šesták, J.; Berggren, G. Thermochim. Acta. 1971, 3, 1–12. DOI: https://doi.org/10.1016/0040-6031(71)85051-7.
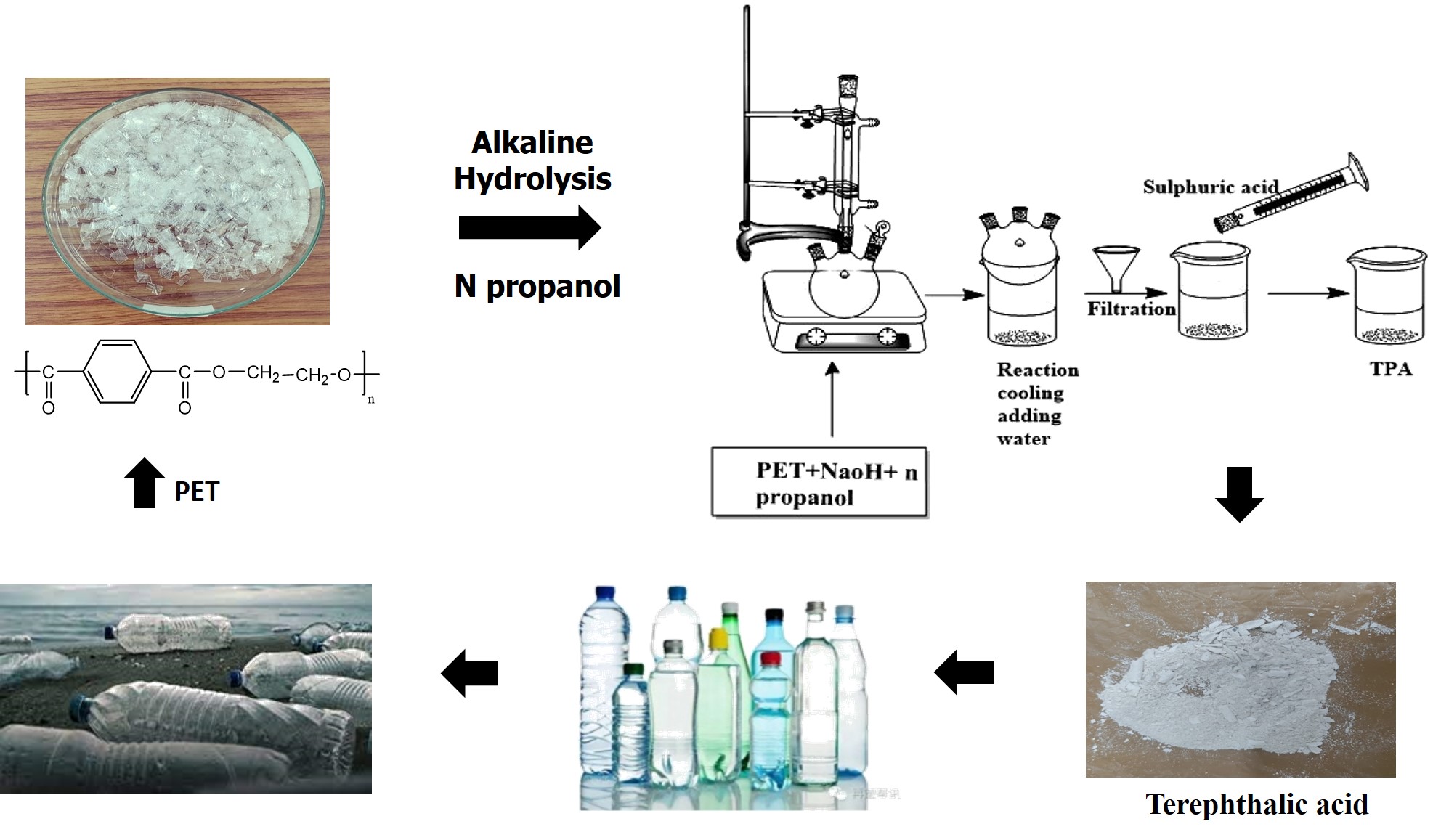
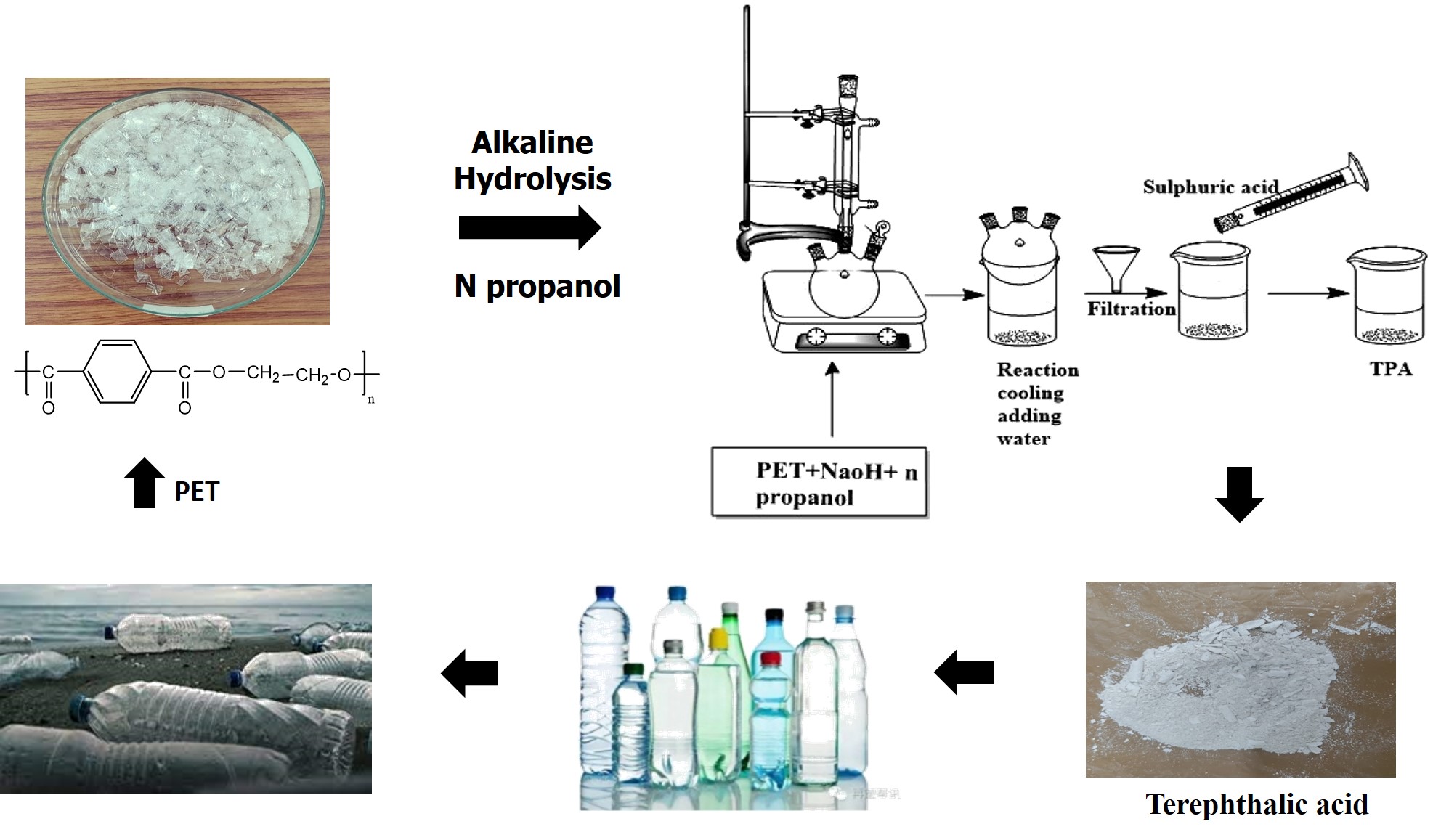
Downloads
Published
Issue
Section
License
Copyright (c) 2025 Gaurav Kumar, Anand Bharti

This work is licensed under a Creative Commons Attribution-NonCommercial 4.0 International License.
Authors who publish with this journal agree to the following terms:
- Authors retain copyright and grant the journal right of first publication with the work simultaneously licensed under a Creative Commons Attribution License that allows others to share the work with an acknowledgement of the work's authorship and initial publication in this journal.
- Authors are able to enter into separate, additional contractual arrangements for the non-exclusive distribution of the journal's published version of the work (e.g., post it to an institutional repository or publish it in a book), with an acknowledgement of its initial publication in this journal.
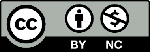