The Effect of Carboxymethyl Chitosan on Calcium Carbonate Precipitation in Synthetic Brines
DOI:
https://doi.org/10.29356/jmcs.v65i1.1429Keywords:
X-ray diffraction, scanning electron microscopy, optical emission spectroscopy of inductively coupled plasma (ICP), scale inhibitor, carboximethyl chitosanAbstract
Abstract. When oil production by natural flow of reservoirs decreases, it is necessary to increase the production by using improved recovery processes, such as water injection. Injection of incompatible water can cause the formation of saline deposits of calcium and magnesium carbonates. The use of chemical inhibitors to treat incrustations involves the use of chemicals with functional groups such as carboxylic acids (R-COOH) or phosphonates (R-PO32-). A new ecological scale inhibitor, carboxymethyl chitosan (CMC1), has been synthesized and its capacity to modify the CaCO3 crystalline phases obtained in the solid residue was compared with that obtained when using a commercial carboxymethyl chitosan (CMC2) and a commercial poly(acrylic acid). The results show that under the used conditions, the CMC´s produce a slightly larger amount of crystalline phases than the synthetic inhibitor. Using the X-ray powder diffraction technique, calcite, vaterite, and aragonite were identified in the residual solid. The ratio of these phases was modified by increasing the concentration of the inhibitor. Using Scanning Electron Microscopy (SEM), it was observed that increasing the concentration of the CMC's the modifies the crystal´s morphology from plates to spheres.
Resumen. Cuando la producción de petróleo por flujo natural disminuye, es necesario aumentar la producción de petróleo crudo y gas mediante procesos de recuperación mejorados. El agua es el líquido que se inyecta y puede provocar la formación de depósitos salinos de carbonato de calcio y magnesio. El uso de inhibidores químicos para el tratamiento de incrustaciones implica el empleo de productos químicos con grupos funcionales del tipo ácido carboxílico (R-COOH) o grupos fosfonatos (R-PO32-). Se sintetizó un nuevo inhibidor de incrustaciones ambientalmente amigable en base a carboximetilquitosano (CMC1), y se compararon las fases cristalinas de CaCO3 obtenidas en el residuo sólido con las obtenidas al utilizar un carboximetilquitosano comercial (CMC2) y un poli (ácido acrílico) comercial. Los resultados muestran que, en las condiciones utilizadas, las CMC producen una cantidad ligeramente mayor de fases cristalinas en comparación con el inhibidor sintético. Mediante la técnica de difracción de rayos X de polvos, en el sólido residual se identificaron las fases: Calcita, Vaterita y Aragonita. La relación de las fases se modificó aumentando la concentración del inhibidor. Mediante Microscopía Electrónica de Barrido (SEM) de los residuos sólidos, se observó que al aumentar la concentración de las CMC's la morfología de los cristales se modificaba de placas a esferas.
Downloads
References
BinMerdhah, A. SPE. 2010, 25, 545-552. DOI: https://doi.org/10.2118/141168-PA
Mpelwa, M.; Tang, S. Petrol. Sci. 2019, 16, 830–849. DOI: https://doi.org/10.1007/s12182-019-0299-5
Rajeev, P.; Surendranathan, A.; Murthy, Ch. J. Mater. Environ. Sci.China 2012, 3, 856-869. ISSN 20282508
Moghadasi, J.; Jamialahmadi, M.; Muller-Steinhagen, H.; Sharif, A. SPE. 2004, 86524 DOI: https://doi.org/10.2118/86524-MS
Li, X.; Gao, B.; Yue, Q.; Ma, D.; Rong, H.; Zhao, P.; Teng, P. J. Environ Sci.China 2015, 29, 124 – 130. DOI:10.1016/j.jes.2014.09.027 DOI: https://doi.org/10.1016/j.jes.2014.09.027
Kumar, S.; K.; Naiya, T.; Kumar, T. J. Petrol. Sci. Eng. 2018, 169, 428-444. DOI: https://doi.org/10.1016/j.petrol.2018.05.068
Wang, S.; Xu, X.; Yang, J.; Gao, J. Fuel Process. Technol. 2011, 92, 486–492. DOI: https://doi.org/10.1016/j.fuproc.2010.11.001
Doshi, B.; Repo, E.; Heiskanen, J.; Sirviö, J.; Sillanpää, M. Carbohyd. Polym. 2017, 167, 326–336. DOI: https://doi.org/10.1016/j.carbpol.2017.03.064
M. de A., R.; Marques, N.; Paulucci, L.; Cunha, J.; Villetti, Castro, B.; Balaban, R. Carbohyd. Polym. 2019, 215, 137–142. DOI: https://doi.org/10.1016/j.carbpol.2019.03.082
Zhu, A.; Chan-Park, M.; Dai, S.; Li, L. Colloid Surfaces B. 2005, 43, 143- 149. DOI: https://doi.org/10.1016/j.colsurfb.2005.04.009
Ge, H.; Luo, D. Carbohyd. Res. 2005, 340, 1351-1356. DOI: https://doi.org/10.1016/j.carres.2005.02.025
Al-Hamzah, A.; Fellows, C.; M.; Desalination. 2015, 359, 22-25. DOI: https://doi.org/10.1016/j.desal.2014.12.027
Chen, L.; Du, Y.; Zeng, X. Carbohyd. Res. 2003, 338, 333–340. DOI: https://doi.org/10.1016/S0008-6215(02)00462-7
Farooqui, N.; Sorbie, K.; Boak, L. SPE. 2014, 174214-MS. DOI: https://doi.org/10.2118/174214-MS
Xiang, J.; Cao, H.; Warner, J.; Watt, A. Cryst Growth & Design. 2008, 8, 4583 – 4588. DOI: https://doi.org/10.1021/cg8006553
Kontoyannis, C.; Vagenas, N. Analyst. 2000, 125, 251–255. DOI: https://doi.org/10.1039/a908609i
Heywood, B. Chem. Mater. 1994, 6, 311-318. DOI: https://doi.org/10.1021/cm00039a011
Muryanto, S.; Bayuseno, A.; Ma’mun, H.; Jotho, M. Procedia Chem. 2014, 9, 69 – 76. DOI: https://doi.org/10.1016/j.proche.2014.05.009
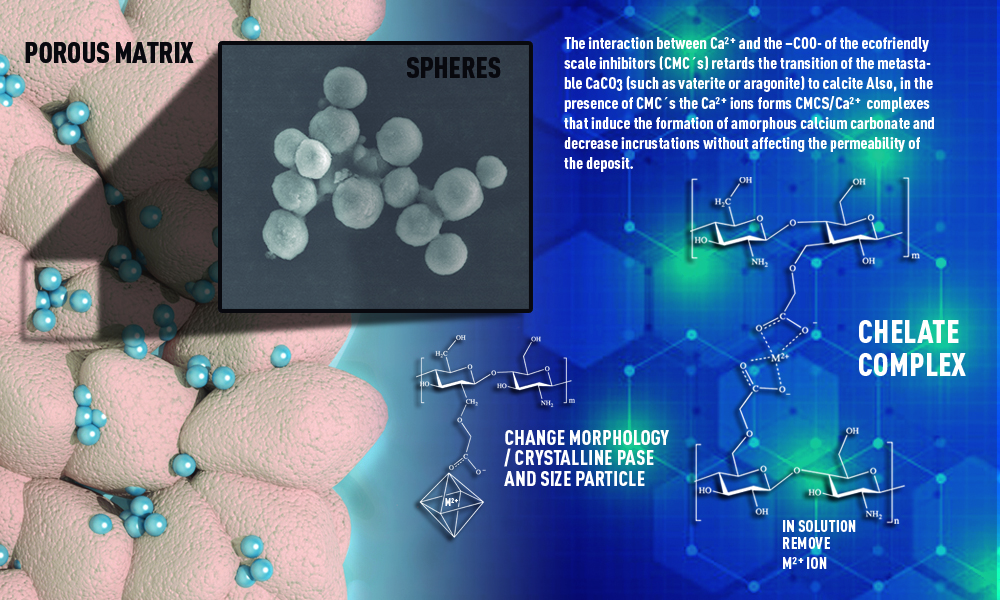
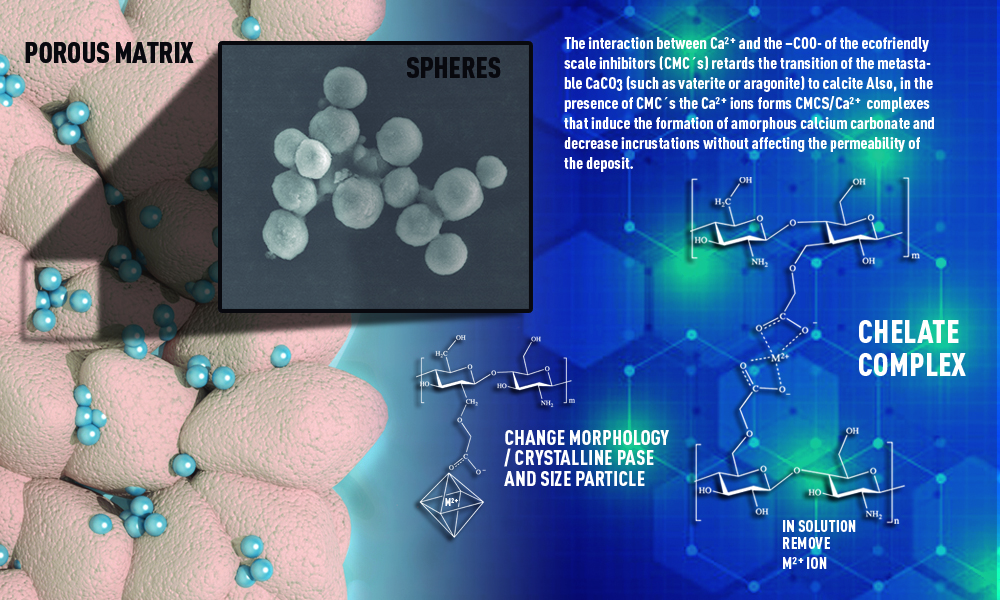
Downloads
Published
Issue
Section
License
Authors who publish with this journal agree to the following terms:
- Authors retain copyright and grant the journal right of first publication with the work simultaneously licensed under a Creative Commons Attribution License that allows others to share the work with an acknowledgement of the work's authorship and initial publication in this journal.
- Authors are able to enter into separate, additional contractual arrangements for the non-exclusive distribution of the journal's published version of the work (e.g., post it to an institutional repository or publish it in a book), with an acknowledgement of its initial publication in this journal.
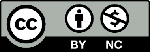